How We Can Create a Better Workforce for the Industry
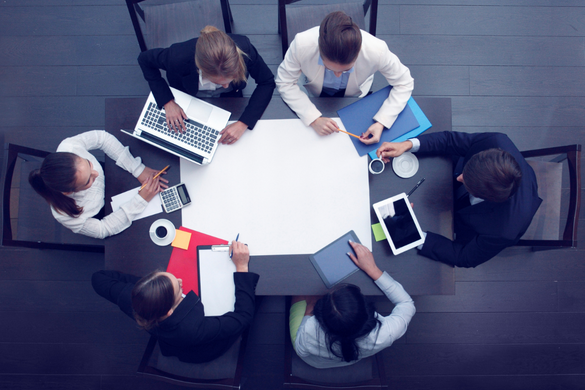
How We Can Create a Better Workforce for the Industry
According to FICCI-A.T. Kearney’s ‘All that Glitters is Gold: India Jewellery Review 2013’, there are gaps in key skills required for modern jewellery manufacturing processes. Some of the key skill gaps which it lists include: Skilled manpower for operating laser machines for cutting and polishing of diamonds; Knowledge of operating computers; Understanding of modern techniques for assortment and planning; Availability of employees who can use design software (CAD) and are aware of international design trends and preferences in jewellery design; Limited manpower capable of using modern machines and understanding modern techniques (for processes such as soldering and plating in jewellery manufacturing).
The Indian Gems & Jewellery industry has so far predominantly run on an on-the-job-training model, and there has been low demand for institution-trained workers among manufacturers. This has kept the cost of labour low for manufacturers, but has resulted in a very slow learning curve, and has also gradually resulted in low attractiveness towards the sector among younger generations of workers. Additionally, sub-scale facilities have contributed to a severe talent shortage.
On the consumption side, patterns of demand are fast evolving, with growing requirements for new designs and higher value addition. Changing customer requirements are increasingly creating a need for a more skilled workforce. Still, around 70 percent of the jewellery processing in India is carried out manually. There is a large gap between demand and skill availability.
Some steps we can take to create a better workforce include:
The first step towards creating a better workforce would be to modernise production processes.
Technology-led innovation is important for the long-term future of any industry. In the jewellery sector, the use of modern design and manufacturing technology can enable jewellers to differentiate themselves, enhance productivity and quality and attract premium prices. The increased profits from technology-led innovation and modernisation of processes itself would attract fresh young talent.
Improving working-conditions would attract more people to the industry. There is limited compliance to health and safety standards in the manufacture of jewellery, especially in the unorganised sector. Most workshops are too small, with karigars working without fans to prevent loss of gold. The jewellery industry should come together to ensure that working conditions of karigars are improved. Creating pooled resources for talent, etc, might help where manufacturers cannot afford to invest in upgraded facilities.
Jewellery manufacturers should absorb graduates from professional educational institutions. While there are institutes that provide courses for the gems and jewellery industry across the value chain, the accessibility to these courses is limited. Course fees are high and the lack of equivalent compensation from the industry reduces their benefit for workers. For example, a professional diamond grading and manufacturing course of 20 to 24 weeks costs about INR 40,800, while a short-term eight-week course on industry-oriented professional jewellery design costs about INR 50,000. A large share of the workforce comes from the low-income segment of the population and is unable to afford these courses. There is a need for the industry to absorption these skilled workers, offering them adequate compensation.
India’s skill development curriculum needs to be standardized and updated to reflect global standards. In the wake of changing customer preferences, artisans should also be encouraged to upgrade their skills through formal training. They could seek scholarships and fee subsidisation. Skill development institutes should have strong collaboration with jewellers to ensure practical training.
Currently, there are around 2.5 million people employed by the industry, of which less than 5 percent are trained through diploma or vocational courses. In the coming five to seven years, there is potential for employment of 0.7–1.5 million additional people. Assuming 10 percent are trained through diploma and vocational courses, the industry needs a training infrastructure to address around 1 lakh new students in the coming five to seven years.
Industry associations and academia have an important role to play in driving consultations for policy making. Universities and research institutions need to be an integral part of initiatives focused on innovation and skill development.
If you have any suggestions for how the industry can improve its workforce, please send them in at info@gematlas.com
(Source: FICCI-A.T. Kearney’s ‘All that Glitters is Gold: India Jewellery Review 2013’)